Denominamos galvanización, a la operación
mediante la cual se aplica por inmersión, una
capa de Zinc sobre una pieza de acero.
El Zinc se encuentra fundido en una cuba o crisol, y en ella se
sumerge la pieza de acero. Con este proceso, se logra dar al
acero base mayor resistencia a la corrosión, (en determinados
medios corrosivos), sin que pierda sus características
mecánicas. En líneas productivas, la
temperatura del baño de cinc, normalmente varía entre 438°C y
460°C. La temperatura máxima del baño, se
establece a fin de preservar la vida útil del crisol, ya que por
encima de 470°C, comienza la etapa de migración acelerada de Fe
de las paredes del crisol hacia el baño. Esto, además de
favorecer la formación de dross, pone la cuba en peligro de
perforación localizada. Los modernos diseños
de los sistemas de calentamiento de las cubas, al calefaccionar
uniformemente las paredes, aumentan notablemente la duración de
los mismos, a la vez que minimizan los riesgos de perforación
por sobrecalentamiento localizado. Al ser de
calentamiento directo y a menor temperatura, (550°C en la cámara
para lograr unos 445° C en el baño), su consumo de energía es
notoriamente menor, y la recuperación de la temperatura en el
baño es más rápida, permitiendo aumentar la productividad del
baño de zinc. A continuación se muestra un
resumen de las etapas y variables que intervienen en este
proceso. El manejo y control de estas variables dará como
resultado final un galvanizado de buena calidad y bajo costo.
En el presente texto no se considera la logística de material,
es decir, las gancheras, su cantidad, su tipo, su diseño, el
método de colgado, cantidad de puentes grúas y/o monorrieles,
estaciones de carga y descarga, almacenamiento, traslado, grúas
horquilla, etc.
-
El proceso previo, (pretratamiento).
-
El secado previo al galvanizado.
-
La temperatura del baño de cinc.
-
La velocidad de descenso y de izaje de las piezas.
-
El tipo de acero de las piezas a galvanizar.
-
La forma y dimensiones de las piezas.
-
El estado de la superficie a tratar.
-
El espesor de las piezas.
-
El tiempo de inmersión.
-
La composición del baño de zinc, (aleantes).
El pretratamiento consiste en sumergir las
piezas en distintos baños químicos y tiene como objetivo
prepararlas para un correcto galvanizado. Consta de varios
pasos, como se ve en el diagrama siguiente:
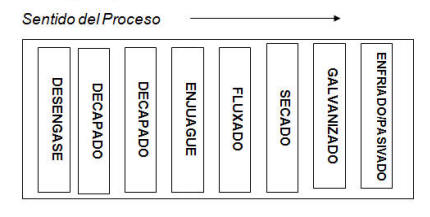
Desengrase
Tiene como objetivo producir la primera
limpieza, eliminando el aceite y las gasas adheridas durante los
procesos de conformación o fabricación de las piezas.
En algunos casos , aún se utiliza desengrases
alcalinos en caliente, pero cada vez es menos frecuente su
utilización, por el alto costo energético de calentar el baño.
La tendencia actual es la utilización de
desengrase ácido, y nuestra recomendación es incorporar HYDRONET,
el cual trabaja en frío, no requiere calentamiento, no requiere
enjuague, actúa como predecapante, acelera el proceso de
decapado, el baño no se descarta nunca, transforma y precipita
las grasas y la superficie del baño siempre está libre de
aceites. HYDRONET no emite olores ni vapores y es absolutamente
seguro al operador y al medio ambiente.
Decapado ácido
El decapado tiene la función de remover los
óxidos que se encuentran en la superficie de las piezas a
galvanizar. Estos se producen durante los procesos previos, o
por la corrosión que se genera durante el almacenamiento,
(corrosión atmosférica).
En el decapado, se puede utilizar ácido
sulfúrico o clorhídrico, (H2SO4 ó HCl).
No se aconseja la utilización de ácido
sulfúrico , por ser más nocivo y peligroso que el acido
clorhídrico, además del costo energético que implica su
calentamiento. Por lo mismo, prácticamente no es utilizado
dentro del proceso de galvanizado.
En la actualidad, la mayoría de los
galvanizadores utilizan HCL en sus decapados. Por sus
características de operación, es imprescindible la utilización
de aditivos. ANTIVAPOR-D es un reductor de emanaciones ácidas,
que reduce hasta en 70% la generación de vapores de HCL, lo que
permite cumplir norma OSHA sin extracción forzada y lavado de
gases, y el Inhibidor IRONSAVE que evita el sobredecapado del
acero, permitiendo dejar piezas dentro del decapado hasta por 36
hrs. sin ataque al metal base.
Enjuague
Es fundamental enjuagar las piezas después de
la etapa de decapado, para reducir al máximo los arrastres de
ácido y hierro a la siguiente etapa.
Es altamente recomendable un doble enjuague ,
idealmente en contracorriente para optimizar los resultados y
reducir el consumo de agua.
Para lograr una mejor cobertura, recordemos
que: “El objeto del decapado será mejor logrado cuando más
limpia esté la superficie de Fe después del mismo y cuanto menos
hayan sido afectadas las superficies y propiedades del Fe por
efecto mismo de dicho decapado”.
Fluxado
El fluxado tiene como objetivos principales
mejorar la interacción entre el cinc y la pieza a galvanizar,
además de impedir la formación de óxidos durante la espera antes
del galvanizado. Adicionalmente, remueve los óxidos remanentes
del decapado.
El fluxado consiste en la inmersión de las
piezas de acero en una solución acuosa, compuesta por cloruro de
cinc y cloruro de amonio, (ZnCl2 y NH4Cl), con un reporte molar
1:2 o comúnmente llamada Sal Doble. Menos usadas son las sales
triples o cuádruples. El rango de temperatura de trabajo es
entre 18° y 70° C. Debido a los costos energéticos, muchos
galvanizadores están optando por trabajar con soluciones a
temperatura ambiente y mayores concentraciones de sales. Solo se
debe cuidar en esta forma de trabajo la adecuada solubilidad de
los cristales de Cloruro de Zinc-amonio.
Después de aplicado el fundente, la pieza es
secada, quedando una película de cristales en toda su
superficie.
La performance está ligada a la temperatura,
la concentración y la relación molar entre los cloruros.
Es importante mantener el baño sin hierro
disuelto, o con un porcentual bajo, (máx. 3.000 ppm.), dado que
influye en el galvanizado posterior, al favorecer la formación
de dross.
El fluxado debe asegurar un tiempo de espera
aprox. de 4 horas sin que la pieza se oxide.
El principal propósito de calentar el fluxado
es que el depósito de sal seque más rápido y explote menos, sin
embargo es mucho mas eficiente y recomendable el secado y
precalentamiento de las piezas.
También en esta etapa se pueden incluir
algunos aditivos como por ejemplo FILM FLUX , que incorpora
Níquel al proceso para controlar el efecto SANDELIN , o METFIL
que reduce las explosiones, la generación de humos y cenizas. La
principal ventaja de estos aditivos es reducir el consumo de
zinc o GZU.
Es altamente recomendable en esta etapa,
filtración continua de la solución.
2.- Secado y precalentamiento
Luego del fluxado y antes del galvanizado,
las piezas deben ser secadas. Este secado le quita la humedad, y
al elevarles su temperatura, favorece el rendimiento térmico del
crisol de galvanizado.
Las piezas deben entrar al crisol totalmente
secas, porque la humedad superficial al entrar en contacto con
el baño produce pequeños estallidos que despiden partículas de
zinc.
Además del peligro para los operadores que
esto significa, provoca mayor consumo de zinc y discontinuidad
en la cobertura.
Se observa que las piezas que entran al baño
totalmente secas, muestran una mejor superficie galvanizada que
las que entran húmedas.
En baños de recuperación lenta de temperatura, el secado, al
elevar la temperatura de las piezas a sumergir en el baño, hace
que la temperatura durante el proceso, se recupere con mayor
rapidez.
Esto trae aparejado un menor tiempo de
recuperación, (o mayor cantidad de piezas a sumergir en el
baño), con un menor consumo de energía por tonelada procesada.
La temperatura a elevar las piezas, no debe superar los 100°C.
El tiempo de secado debe ser el máximo
posible con un tope de una hora.
La capa de Sal Flux se degrada sobre los
120°C, por lo que no se debe sobrepasar ese limite de
temperatura para mantener las propiedades y beneficios del
fluxado.
La temperatura del baño de cinc tiene fuerte
incidencia en el espesor de la cobertura.
Ensayos realizados con chapas cortas y planas
de igual espesor, (2,5 mm), galvanizadas a distintas
temperaturas, dieron espesores de coberturas menores para las
temperaturas más bajas.
La cobertura de las chapas galvanizadas a
menor temperatura, fue un 16% menor, (878 g/m2 versus 1026
g/m2).
En general se nota que el espesor de la
cobertura, luego de superar los 451°C, comienza a crecer más
lentamente.
Las distintas pruebas realizadas, (con el
baño entre 442°C y 460°C), mostraron que las menores coberturas
se lograron con las temperaturas más bajas.
Es importante que el diseño del calentamiento
del crisol, permita trabajar continuadamente a las temperaturas
más bajas. Esto favorece la uniformidad del galvanizado, la
mayor duración del crisol y la menor cobertura a lograr.
4.- Velocidades de descenso y de izaje de las piezas
Ambas velocidades tienen importancia en el
espesor de la cobertura lograda. La de izaje, cuanto más baja
sea, nos permite un mayor escurrimiento del zinc sobre la pieza
galvanizada. La de descenso, (que debe ser lo más alta posible),
permite que el tiempo total de inmersión de la pieza, sea menor.
Esta velocidad de descenso “lo más alta
posible”, tiene la limitación de las piezas con formas que
puedan ofrecer resistencia a la penetración en el baño; es que
al entrar a velocidades altas, se desprenden de los ganchos al
chocar con la superficie de cinc líquida.
Para galvanizado de piezas con formas que
afectan su rápida penetración, son usuales velocidades de
inmersión entre 3 y 4 m/min.
La velocidad de izaje para piezas que
penetran más de 400 mm., también está influenciada por el mayor
tiempo de inmersión de la zona más baja, (la que entra primero),
con lo que se deberá encontrar una velocidad que tenga en cuenta
ambos factores.
Dado que en este tipo de galvanizados la
parte que entra primero al baño, es la última en salir, se
produce una diferencia notoria en el espesor de cobertura entre
la parte inferior de las piezas y la parte superior. Esto es
producto del mayor tiempo de inmersión que pasa dentro del
crisol la parte inferior, y será más importante la diferencia
cuanto más larga sea la pieza.
En general se recomienda una velocidad de 0,6
a 0,8 mts./min.
También se debe tener en cuenta:
4.1) Se pueden mezclar piezas de largos
diferentes, y espesores distintos en cada carga, para aumentar
el índice de productividad.
4.2) Se debe limpiar la superficie el baño
antes de sumergir cada carga, para evitar que la ceniza que
sobrenada en la superficie, se adhiera a las piezas.
4.3) Antes de comenzar a retirar la carga,
se debe limpiar nuevamente la superficie, para quitar las
impurezas y cenizas sobrenadante.
4.4) La limpieza de la ceniza en superficie
SIEMPRE debe ser efectuado en forma suave y regular, para evitar
las “olas” que generan una cobertura discontinua y contribuyen a
la formación de óxidos de zinc y ceniza
Mientras son izadas las piezas, se debe
continuar limpiando para evitar que las cenizas que se forman se
adhieran a las piezas.
5.- El tipo de acero de las piezas a galvanizar
Bibliografía especializada, indica que el
aumento del tamaño de grano en la chapa base favorece el
incremento de la velocidad de difusión, lo que finalmente
aumenta el espesor de la cobertura.
De acuerdo a lo mencionado, en iguales
condiciones de galvanización, se obtendrán menores coberturas,
cuando la chapa base tenga un tamaño de grano menor.
De igual manera, superficies menos rugosas
nos darán también coberturas menores.
También se indica que el Silicio, el Carbono
y el Fósforo en el acero, tienden a aumentar el espesor de las
fases de aleación hierro-cinc.
Dado que, el tenor de Si en la chapa base,
influye notoriamente en el peso de la cobertura, se analizará
particularmente.
En la curva de Sandelin - Rothauser, se ve
claramente como aumenta la cobertura, entre porcentuales desde 0
a 0,05% de Si en peso. Además, muestra las variaciones logradas
en las coberturas según las distintas temperaturas.

La anterior figura es la Curva de Sandelin,
trazada por Rothauser, donde se nota la influencia en la
cobertura del porcentaje del Si de la chapa base, y a su vez la
variación que sufre la cobertura en función de la temperatura
del baño.
Tomando como ejemplo la mencionada curva,
vemos como a igual temperatura del baño de cinc (452°C) el
contenido de Si, influye sobre el revestimiento. Con un
contenido de Si, de 0,01% observamos que el recubrimiento
promedio es de más de 70 micrones (994 g/m2). Mientras que con
0,03% de Si, el recubrimiento alcanza aproximadamente 160
micrones (2.270 g/m2). Prueba realizada en chapas por lo que en
el calculo de peso de zinc se consideran las dos caras. Por lo
tanto se muestra gráficamente, la notable incidencia que el Si
tiene en el espesor final de la cobertura.
El gráfico que seguidamente se muestra,
relaciona peso-tiempo del recubrimiento y tipo de acero a una
temperatura de galvanizado de 445°C.
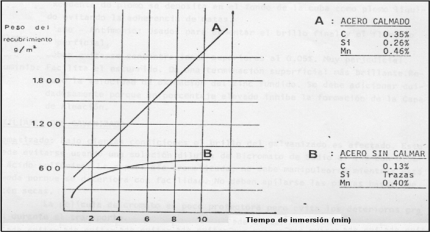
Como regla general, para lograr coberturas
menores, la chapa base debe tener el silicio en valores lo más
bajos posibles, en nuestro caso cercano a 0,01% en peso, y la
temperatura del baño debe ser lo más baja posible, (alrededor de
440°C).
Una alternativa para controlar el efecto
Sandelin es agregar Níquel metálico en toda la cuba de zinc
fundido y la otra es agregar el Níquel en la etapa de fluxado,
con lo que el níquel solo se deposita en la superficie del acero
que es donde tenemos el problema de reactividad.
6.- La forma y dimensiones de las piezas
La forma de las piezas a sumergir en el baño,
tiene incidencia en la cobertura a lograr. Dos chapas sin
curvar, de ondulación y dimensiones iguales, si se sumergen una
“parada” y la otra “acostada”, tendrán distinta cobertura.
La chapa “parada”, tendrá menor cobertura,
por el mejor escurrimiento del baño.
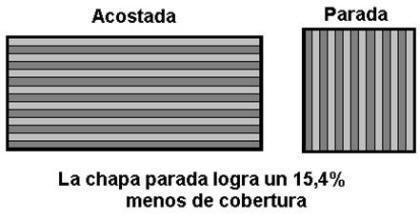
A su vez, dos chapas de iguales
características de ondulación y dimensiones, pero una de ellas
curvada y la segunda corrugada plana, la pieza curvada, tendrá
mayor cobertura, por el efecto “cuchara”.
Esta cobertura, será mayor, cuanto menor sea
el radio de curvatura.
A la vez, los radios menores, hacen necesario
que la velocidad de descenso en el baño sea menor, por el riesgo
de desenganche de las piezas, (aumento del tiempo de inmersión
de la parte inferior de las piezas).
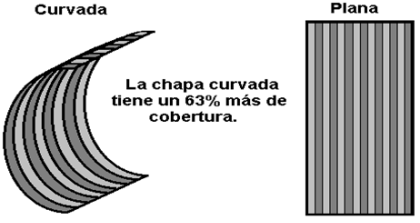
Finalmente, las formas que favorecen el
escurrimiento del baño, disminuyen el espesor de la cobertura.
También la longitud de las piezas incide en
la cobertura, dado que al aumentar el espesor en los sectores
inferiores, aumentará el promedio total de la cobertura.
7.- Estado de la superficie a tratar
Las piezas que deben regalvanizarce, tienen
su superficie atacada por el decapado en forma discontinua. Debe
evitarse al máximo el reproceso por la negativa incidencia en
los costos de producción.
Será mayor el ataque, por el aumento del
tiempo de decapado, profundizándose esto, en las zonas donde
haya menor cobertura inicial.
También incide la cantidad de óxido
superficial que tengan las chapas, que además de degradar en
mayor medida el baño, incidirá en la calidad de la superficie de
las piezas.
Las piezas que tengan mayor oxidación y/ó
rugosidad tendrán a su vez, mayor cobertura.
8.- El espesor del acero de las piezas
Al efectuar una experiencia práctica para
verificar la incidencia del espesor del acero en el consumo de
Zinc, se pudo verificar claramente que para una misma
temperatura de galvanizado (448°C), la piezas de mayor espesor
de acero tienen una mayor absorción de Zinc.
La desviación de la tendencia que se produce
en los valores mínimos, puede estar asociada a la composición
del acero y a la geometría de algunas piezas.
Entre extremos, tomando los espesores 1,6 mm.
y 6,9 mm., la cobertura es 40,54% mayor en la de mayor espesor.
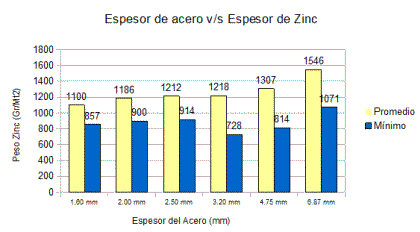
También es de vital importancia considerar el
espesor del acero en los cálculos de GZU, pues al final la
absorción del acero será por la superficie total de la pieza y
esta será mayor o menor dependiendo del espesor. Para una ton de
acero de 2 mm. se estima un superficie de 128 mts2 , en cambio
para una ton de acero de 6 mm. de espesor la superficie será
apenas de 42 mts2.
Para calcular la superficie de una ton de acero en relación
al espesor del material, se puede utilizar la siguiente formula.
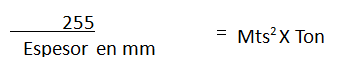
9.- El tiempo de inmersión
El tiempo de inmersión, juega un papel
importantísimo en el espesor de la cobertura. A mayor tiempo de
inmersión se verifica una mayor cobertura.
A continuación se indican resultados de
experiencias reales en plantas de galvanizado.
9.1) Con chapas planas, de 2,5 mm. de espesor, de 200 mm. por
200 mm., de igual composición y rugosidad, con igual velocidad de
izaje, (1,5 m/min), y a igual temperatura del baño (445°C),
sumergidas en igual posición del crisol, pero con tiempos de
inmersión distintos.
Para cada ensayo se usaron 3 probetas. Se tomaron 30
mediciones en cada caso, (10 por probeta).
Se arribó a los siguientes valores según el tiempo de
inmersión:
9.1.1- Normal, (hasta que cesó el burbujeo). Promedio
68,80µ=982 g/m2 (dos caras).
9.1.2- Normal más 1 minuto. Promedio 82,60µ=1179 g/m2 (dos
caras).
9.1.3- Normal más 2 minutos. Promedio 98,50µ=1406 g/m2 (dos
caras).
9.1.4- Normal más 3 minutos. Promedio 100,0µ=1428 g/m2 (dos
caras).
9.1.5- Normal más 4 minutos. Promedio 102,9µ=1455 g/m2 (dos
caras).
La diferencia en el espesor de la cobertura
que se observó entre la chapa con el tiempo de inmersión normal
y la sumergida con 4 minutos más, fue casi 50% mayor.
9.2) Con caños sin costura de diámetro interior 130 mm, de
6,35 mm de espesor y cortados 300 mm de largo, (todos del mismo
caño madre). Se galvanizaron siguiendo el siguiente esquema en lo referido a
los tiempos de inmersión:
9.2.1- Normal (hasta que cesó el burbujeo). Promedio
65,3µ=932 g/m2.
9.2.2- Normal, pasada dos veces por el crisol. Promedio
143,9µ=2054,6 g/m2.
9.2.3- Normal más 3 minutos. Promedio 104,4µ=1491,4 g/m2.
9.2.4- Normal más 10 minutos. Promedio 450µ= 6426 g/m2.
9.2.5- Normal más 15 y 30 minutos. Promedio superior a 7200
g/m2 (fondo de escala).
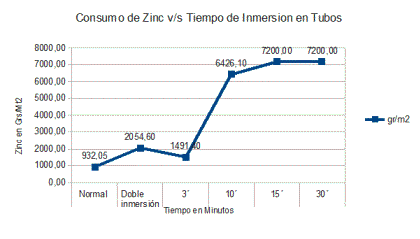
Es notable la diferencia de cobertura que se
logra al pasar la misma pieza dos veces por el crisol de
galvanizado, (duplicó la cobertura).
Esta incidencia del tiempo de inmersión en el
crecimiento de la cobertura, hace que se deba buscar una
velocidad de descenso y de izaje que compatibilice la diferencia
de cobertura entre la parte inferior y la superior de la pieza
galvanizada, logrando la menor cobertura posible, compatible con
la mayor producción.
En todo caso, es absolutamente desaconsejable efectuar
galvanizado por doble inmersión, debido a la perdida de
productividad y alto costo que esto implica.
10.- La composición del baño
La influencia de la composición de metales en
el baño de galvanizado, tendrán diversos efectos, dependiendo de
la concentración de cada uno.
Normalmente, aparte del zinc, se puede
agregar al baño plomo, estaño, aluminio o bismuto.
Características particulares del
galvanizado Batch (recopilación)
Vista esquemática de una chapa de acero galvanizada por
inmersión, (tipo Batch)
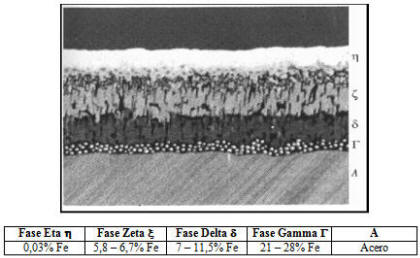
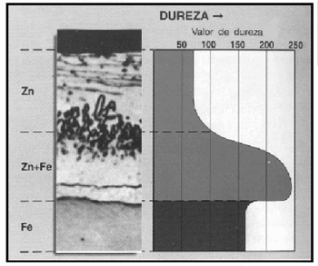
Zonas desnudas
Una pequeña área expuesta de un recubrimiento
de zinc sobre una pieza de acero, es protegida por el carácter
de sacrificio anódico del depósito de cinc.
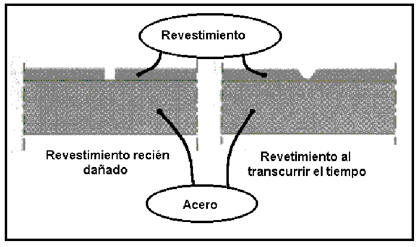
El cinc que rodea la zona “desnuda”, se corroe.
Los productos de la corrosión precipitan
sobre la superficie del acero base protegiéndolo.
También en el caso de deformaciones en
productos galvanizados que puedan producir “grietas”, estas se
“llenan” con productos de la corrosión, y el carácter de
sacrificio anódico del depósito de cinc, continuará
protegiéndolo en las grietas producidas.
Lo característico de la protección galvánica,
resulta del hecho que el cinc es más activo electroquímicamente
que el acero.
Las zonas desnudas en una pieza galvanizada,
cuando se deban a defectos de laminación, (cascarillas que se
desprenden al galvanizar), no son motivo de rechazo, y pueden
retocarse con pintura rica en cinc.
Duración y uniformidad del recubrimiento
El tiempo que una pieza galvanizada puede
durar, entre otras variables, será función del ambiente a que
esté expuesta.
Para ambientes de iguales características,
será mayor su vida útil, cuanto mayor sea su cobertura.
Ambiente
|
Duración estimada de un
recubrimiento de 600 g/m2 (años) |
Rural |
34 |
Marino |
23 |
Industrial |
20 |
Industrial contaminado |
5 |
Deformación
Para piezas soldadas que deban galvanizarse,
se recomienda precalentar adecuadamente para disminuir las
tensiones de soldadura, y para reducir al mínimo el alabeo y
deformación.
Lo ideal sería que las partes fueran del
mismo espesor y con secciones simétricas.
En caso de piezas cerradas, o con cavidades
herméticas, nunca deben incluirse en el material a galvanizar.
Una picadura en la soldadura permitiría que la solución del
pretratamiento se infiltre en la cavidad. En la inmersión en
cinc fundido, el vapor generado no podrá escapar rápidamente,
generándose presión, con su respectivo peligro de explosión, y
riesgo de accidentes severos. Para estos casos , se deben
efectuar las correspondientes perforaciones.
Inspección superficial del galvanizado
La rugosidad superficial, los granitos,
(partículas ocluidas), colgantes o colgajos, manchas de color
gris oscuro, manchas blancas de óxido blanco, no serán motivo de
rechazo, dado que no afectan las propiedades del recubrimiento,
salvo que hubiera un acuerdo previo en contrario.
Consideraciones sobre el galvanizado y el crisol
El punto de fusión del cinc es de 423°C,
comenzando su solidificación alrededor de los 419°C.
No es conveniente dejar solidificar el baño
dentro del crisol, dado el riesgo que significa el refundido del
cinc en las soldaduras e la cuba.
El crisol de galvanizado debe ser
inspeccionado regularmente. Si la pared, sufre un adelgazamiento
en áreas importantes, que lleva su espesor a 25 mm o menos, se
deberá desechar.
Es de notar que la resistencia a la tracción
admisible en el acero, va disminuyendo paulatinamente a causa de
la temperatura a que es sometido el crisol en el proceso de
galvanizado, y al cabo de unos 10 años, ha llegado a ser tan
baja, que las tensiones de tracción existentes en las planchas
no pueden ser ya absorbidas y el crisol puede romperse
súbitamente.
En crisoles calentados por conductos, también
se deberá tener cuidado cuando las paredes tenga una deflexión
superior a los 30 mm. por lado.
El aluminio adicionado al baño, no debe
superar el 0,01%, dado que favorece el ataque a las paredes del
crisol, a la vez que en porcentajes superiores, puede conducir a
la aparición de puntos sin recubrimiento.
Dross
El cinc contenido en el baño dentro del
crisol está en constante circulación.
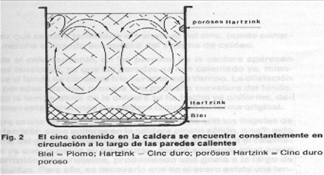
Las partículas de Fe de la pieza, del
desprendimiento de las paredes del crisol, y del pretratamiento
en combinación con el baño fundido, hacen que este se sature de
hierro, (0,018% a 450°C), y el exceso forma el dross que
precipita cristales hierro-cinc. Dado que son levemente más
pesados que el cinc, estos descienden y se van depositando
lentamente en el fondo del crisol.
Es conveniente que el dross depositado en el
fondo no supere una altura de 250 mm. Las temperaturas altas de
galvanización mantienen más dross en suspensión que las
temperaturas bajas, (el dross en suspensión incide en la calidad
superficial).
En algunos casos, en este tipo de crisoles,
en el fondo se cubre los 300 mm inferiores con ladrillos
refractarios para proteger la zona donde se acumula el dross.
Este dross es rico en hierro, lo que produce que esté a mayor
temperatura que el baño de cinc , por lo que si no tuviera esta
protección, las paredes del crisol se deteriorarían rápidamente.
Es conveniente mantener el dross lo más bajo
posible, siendo algo bueno, hacer extracciones semanalmente. Los
cristales que flotan, producen inclusiones en el recubrimiento,
que perjudican el aspecto superficial de la cobertura. El
mantener bajo el dross, además favorece la mayor duración del
crisol.
Las extracciones de dross deben hacerse con
el baño a temperaturas del orden de los 434°C.
La generación de dross y ceniza, es
aproximadamente entre 20% - 25% del cinc utilizado, contándose
ambas en proporciones que van de 1:1 a 1:2 dependiendo del tipo
y control de proceso.
La ceniza contiene de un 70 a 80% de cinc
metálico, mientras que el dross entre un 90 y 95%.
Es posible reducir la cantidad de ceniza
generada, utilizando aditivos al Fluxado y recuperadores en el
baño de Zinc Fundido.
Agradecimientos
Este material ha sido preparado, actualizado y adaptado
por Ricardo Pérez M. en base a la colaboración efectuada por el
Ing. Sr. Luis Padua.
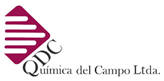
Otros artículos de
interés:
Galvanizado en
Caliente y en Frío
|